Generally speaking, the investment in stamping production equipment and mold tooling is high, and both equipment and mold tooling have depreciation and service life. If the equipment is idle and cannot be fully utilized, it will undoubtedly be a huge problem for vehicle manufacturers. waste. Therefore, all major vehicle manufacturers are striving to make the press line run at full capacity as much as possible without affecting the production plan, and outsourcing preparations for parts that exceed the load capacity in advance.

Stamping Capacity Analysis Method
Usually, stamping capacity analysis is mainly about the collection and calculation of key stamping capacity parameters. The following is an example of five stamping lines in FAW Jiefang’s stamping workshop. Line A is an automatic line and the rest are manual lines. The standard working time of 8 hours and 250 days of annual work is the premise of the analysis. The key production parameters of these 5 stamping lines are analyzed by example, and the production parameters are briefly explained, as shown in Table 1.
⑴ number of consecutive strokes. The number of continuous strokes refers to the number of strokes per minute of the entire line during continuous production of the stamping production line. Usually, the number of continuous strokes for parts on a manual stamping line is relatively close, while the number of continuous strokes for parts on an automatic stamping line is quite different. , at this time, the number of continuous strokes of each workpiece needs to be averaged according to the proportion of output as the number of continuous strokes of the entire line.
⑵ mold change time. Taking “shift” as the calculation unit and “month” as the basic consideration time, count the number of mold changes per shift and single mold change time in the past three months, and obtain the average number of mold changes per shift and single mold change time for the entire line. Die change time. A single die change time can be divided into technical die change and production die change.
⑶ Mobility rate. Mobility rate = (working time – mold change time – stop time) ÷ working time. Here, the mold change time is used as a parameter to be considered, because there are relatively few factors affecting the mold change time, and it is relatively easy to control.
⑷ Effective stroke number. The number of effective strokes = the total number of strokes in a single shift ÷ the working time of a single shift. The number of effective strokes, as the “result” parameter of the stamping production line, is the value that best reflects the level of stamping production capacity, and should be controlled and managed as the KPI assessment index of the stamping workshop.
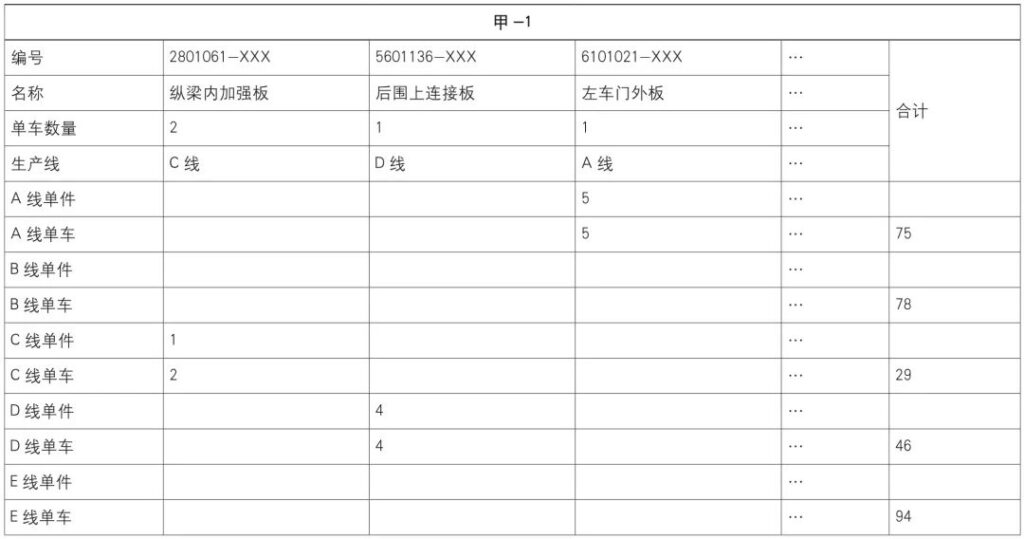
Table 4 Statistical table of the number of strokes for a bicycle of model A
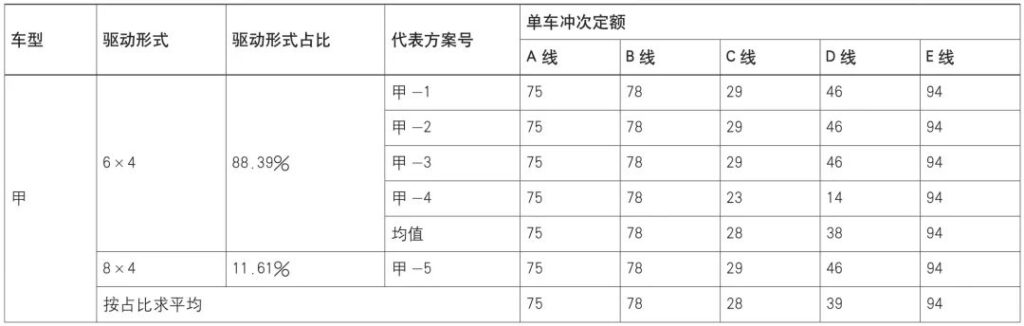
Table 5 Summarization of the quota for the cycle times of the whole line
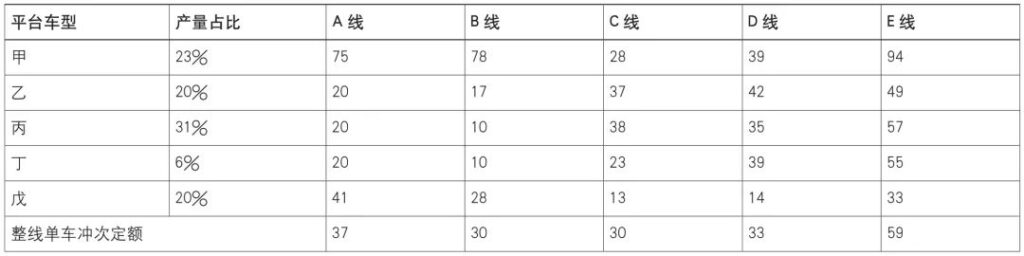

Common stamping demand forms
There are two common forms of stamping demand, namely annual output and daily output. Annual output is generally used for long-term planning and analysis, while daily output is generally used for short-term market situation change analysis, see Table 6.
Establish stamping capacity and production load calculation template
The stamping production load calculation template is based on Excel, supplemented by some simple formulas. The establishment process of the calculation template is as follows:
⑴Create an input interface for analysis premise. The premise mainly includes production premise and working time premise. The production premise includes daily output or annual output. The working time premise is divided into standard working hours and limit working hours. 3 shifts of 300 days, the specific calculation should be input according to the demand. Figure 1 shows the daily output demand of standard working hours.